Kiss goodbye to paper and say Hello to Smart Warehouse Management
Warehouse Management made easy from now on, and ready to boost your eCommerce startegy. 100% Paperless Technology means No more mis-picks or mis-ships.
Pick, Pack and Ship Faster with confidence.
Get a Demo

Your Operations
100% Paperless

Built-in
Quality Control

Pick, Pack &
Ship Faster

Smart Receiving
& Inspection
Warehouse 100% Paperless
Hexoss was made with saving you money and preserving the environment in mind. Why print a purchase order when you receive a delivery, or a picking list, when you have to fulfill orders? There is no real need, if you your company runs on an efficient software, and here we are.
No more delays in your fulfillment process because of a jammed printer, no need to come earlier to print orders in batch, no more order shipped with a missing product because the SKU and location was printed so small that your employees started to mix them up. Even the inspection of your deliveries, can be done without paper and error free.
Thanks to our powerful, real time, technology and our heavily studied ergonomic, no more needs of long and boring training.
Don't be fooled by the other guys, they will talk about "User friendly" but when you will start to use their software, you will also need to take an aspirin! With Hexoss, you will just be pleased to finish your day earlier, headache free with happy customers. Try it for free and you'll understand.
Order Fulfillment that fit your business needs
Choose between: "Pick and Pack" or "Batch picking". If you are a wholesaler and each order requires one employee's attention to be fulfilled, you will choose "Pick and Pack".
Your warehouse workers will fulfill orders, one at a time. But if you sell in retail, you can take benefit of a batch picking that will allow your workers to pick several orders in only one optimized trip.
Pick N Pack
Assuming, you handle large orders per customer and you dedicate a worker for each order. So get a barcodes based picking with optimized path and quality assurance directly embedded into the picking job.
100% paperless, your picker will be guided step by step to pick each product, pack them and keep track of serial and lot numbers that were packed into a specific box or pallet.
Your order will be ready to ship with accuracy and ease, no matter if it's made of a single or many packages. Packages' weight will be automatically calculated.
Batch Picking
If you sell in retail, that means you have to handle many orders with just a few products for each one of them and you cannot handle them one by one. It's such a waste of time and money.
Become more efficient by adopting our 100% paperless barcodes based Batch picking. Our system will regroup SKU required to fulfill multiple orders together and then optimized and guide your picker to make only one efficient trip with no back and forth useless walk.
With our, "Drop into Tote" technology, each picking is optimized one more time, because each tote was assigned to one order and at the end of the trip you will get all your orders consolidated, ready to be packed and shipped.
Packing
No matter which type of picking you have chosen, you can pack each order into one or several packages and keep track of their contents, directly accessible from the order you will keep track of Lot and serial numbers. In the case of package lost, you will be able to identify which products are eligible for a refund or need to be sent again.
Did you know?
Each mistake made during picking & packing processes, cost you at least $50. With Hexoss you will be able to save $10,000 a year or more.
Workforce management 2.0
Managing a warehouse is time consuming and not hassle free. Your manager needs do dispatch the workload and ensure that everybody is on task, keeping up on deliveries and inspections. He or she needs to stay on schedule even if someone is out sick.
How about getting some help with a smart assistant that would ensure everybody is busy and efficient. Your manager will simply have to assign your workers a task like picking, packing or shipping. Meanwhile other will perform the replenishment or handle the customer returns. And then, no need to micromanage your team. They just have to check notifications and start their tasks, as they will automatically pop up. If a delivery comes up, they can receive and inspect it now or later.
No more delivery received and forgotten in the back of your warehouse, you keep track of everything and run your warehouse operations smoothly and hassle-free.
Pickup Order
You can offer your customers the convenience to pick up their order and avoid shipping fees. We made it simple.
If the order was set to pickup, you fulfill it like all other orders. At the shipping station it will automatically popup as "Pickup Order" and a label will be automatically printed to identify the order in you facility.
We take care of notifying your customer by email that his/her order is now ready and available for pickup.
Receiving Delivery
100% paperless and barcodes accelerated. Know exactly what deliveries are planned at each warehouse. In one simple dashboard, spot what deliveries are late, what is scheduled for today and how many received deliveries are awaiting for inspection.
When you receive a delivery, you can choose between check it now or later. Your employees will timestamp the delivery and fill out the type and how many packages they received. So you know it's in the warehouse even if it's not yet inspected.
Smart Delivery Inspection
Inspecting a delivery is very time consuming and error prone. Your employees used to count and recount the merchandise to ensure the delivery is ok.
Sometimes the same SKU can be spread among multiple packages and losing count can happen very quickly and delay the complete inspection. If you add the lot or serial numbers to the inspection, it can turn out to be a real nightmare.
Make multiple workers inspect the same delivery, will get your team more confused than really speeding up the process, but that was before.
With our advanced, 100% paperless, delivery inspection technology your staff member doesn't need to keep the count of each SKU, we'll handle it. They just add up what they found inside the packages as they go and we consolidate the quantities per SKU.
If there are serial numbers to handle, simply input how many to add up and then scan all serial numbers, one after another and don't worry we will detect if there is any duplicates.
If they have to check a SKU with lot numbers just enter the lot number and select the expiry, if any, then input the quantity found.
If they found more quantity later for the same lot, no need to re-enter it, just from a fingertip, tap on one of our lot number shortcuts and speed up the inspection.
And the best part for you and your manager, is that you can get the real time tracking of what has actually been inspected by simply opening the purchase order.
Smart Put Away
Now that your delivery has been inspected, it's time to put it away as quick as possible to make your merchandise available for immediate sale.
And once again, it's going to be so easy. Just flag that the inspection as complete and we will instantly create, your putaway jobs.
If you manage overstock bin, we will automatically spread the received quantity to refill your picking bin, then put the rest in overstock.
Our put away trip manager allows you to select what you want to carry in one trip, to split quantity or change the destination in a snap.
Smart Replenishment with 2 bins location
You manage a picking and an overstock bin for a SKU. Simply set the minimum quantity that your picking bin should hold.
If the quantity on shelf falls below, it will automatically trigger a replenish job. Your worker will be guided to the overstock bin to pick the required quantity and then will be guided toward the picking bin to put it away. Managing replenishment has never been so easy.
Moving products location
Time to time it can happen that you need to move a product from the shelf A toward the shelf B. It's very easy, in fact, you just have to change the bin location of your product. If you have some inventory there, it will trigger a "move job" immediately available for your workers. And they will be guided from shelf A for pickup then guided toward shelf B to put them away.
Cycle count
Stocktake requires a lot of resources, is time consuming and frustrating because you are shutting down your whole warehouse operation.
Thanks to our multi-level stock control, you can now perform cycle counts with NO downtime. You will just need to lockdown one SKU at a time.
You don't have to choose between stock accuracy and warehouse efficiency anymore , now you can check your inventory as you wish and at your own pace.
Reverse Logistic
Process your customer's return faster. Scan the barcode on the Return authorization sent to the customer and the complete return will show up with expected products and quantity.
Your staff member will be able to check the goods and restock it. Your customers will be automatically notified that their return has been received and processed.
Product Locator
Found a product on the floor or left on a cart and don't know where it belongs? Easy! Just scan the barcode into our product locator and you'll instantly get the exact bin location.
Multi-Warehouses / Multi-Stores
Create and Manage unlimited Warehouses/Stores. Each of them has their own stock levels, costs of good, triggers, and bins Location.
For example, you can handle cases, like having 2 warehouses or having one distribution center and 3 stores.
No matter what the context you will be covered, and obviously, we will keep up with your growth. Just add your next successful location at no extra cost.
Transfer between Warehouses
Transfer your products from a warehouse to a store or between warehouses with ease. Simply create a transfer and indicate origin and destination, then add your product the same way you make a purchase order.
The transfer will reserve product quantities at the origin warehouse and show them up as incoming at the destination warehouse.
An assistant will guide your worker to pick the products needed to fulfill the transfer. Once shipped to the destination they will be received and checked like any other Purchases Order. Put away jobs will be automatically generated to ensure availability on shelf of your transferred products at the new location.
The process is totally assisted from end to end. You will speed up your transfer, and keep track of them, until completion and ensure that will be done, mistakes free and 100% paperless.
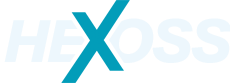
8383 Whilshire Blvd
Suite #740
Beverly Hills,
CA 90211
© - Hexoss Inc.
All Rights Reserved.
We use cookies to give you the best experience. By continuing to browse this site, you give consent for cookies to be used. For more details please read our
Privacy Policy.
I agree